MIM-technologie
SPUITGIETEN VAN METALEN
MIM-proces
Dankzij de metaalspuitgietprocessen van de Zimmer Group zijn er geen grenzen gesteld aan de productie van geavanceerde werkstukken. Complex gevormde serie-onderdelen van metaal gaan vaak gepaard met een meerlaagse productie-inspanning. Het MIM-proces gaat dit tegen en maakt het mogelijk metalen onderdelen met behulp van spuitgieten in vrijwel elke vorm te produceren, waarbij de geometrische vrijheid van kunststofspuitgieten wordt gecombineerd met de sterkte en slijtvastheid van metalen.
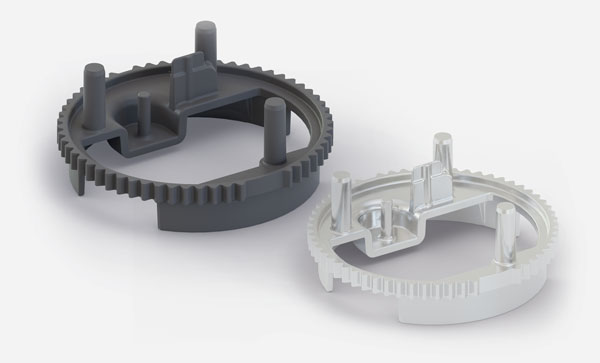
De MIM-technologie biedt u dus een groot aantal overtuigende voordelen:
- Rendabele serieproductie van complexe metalen componenten
- Ontwerpvrijheid bij de ontwikkeling van uw componenten of samenstellingen
- Materiaalvrijheid: roestvrij staal, laaggelegeerd staal, HSS-staal, evenals harde metalen, titanium en titaniumlegeringen en zware metalen
- Serieproductie van onderdelen met een gewicht van 0,3 g tot 150 g stukgewicht
- Complexe onderdelen met wanddiktes tot 0,2 mm kunnen worden gerealiseerd
- Boringen, inwendige en uitwendige schroefdraad, ondersnijdingen en vertandingen
- Mechanische sterkte en bewerkbaarheid, zoals bij conventioneel vervaardigde werkstukken
- Oppervlaktebehandeling door vibratieslijpen, spiegelpolijsten, zandstralen, passiveren, elektrolytisch polijsten of beitsen
- Coaten door polijsten, chromateren, verkoperen, vernikkelen, verzilveren of vergulden
- Vermijdt productiekosten door besparing van kostenintensieve montage- en verbindingstechniek
- Bij complexe componentgeometrieën ca. 25% tot 65% goedkoper dan conventionele productieprocedés
- Toepassingsgebieden zijn overal te vinden waar kleine complexe metalen serieonderdelen worden gebruikt, zoals in tandwielonderdelen, de horloge-, juwelen- en brilindustrie, in medisch-technische onderdelen, in werktuigbouwkundige en handlingonderdelen, in kleine onderdelen voor mobiele telefoons, computers en andere toestellen.
Materiaaleigenschappen-pdf
MIM – Het proces
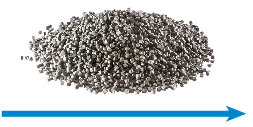
Grondstof
Het uitgangsmateriaal voor het spuitgieten van metaalpoeder is de zogenaamde "feedstock". Dit bestaat uit ongeveer 60 vol.% van het desbetreffende metaalpoeder en 40 vol.% van een bindmiddel, d.w.z. een mengsel van polymeren en was. De homogene menging van alle componenten is van centraal belang, aangezien alleen op die manier een optimale verwerking en een constante productkwaliteit in het daaropvolgende proces kunnen worden gewaarborgd.
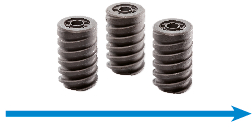
Spuitgieten
De grondstof wordt op dezelfde wijze verwerkt als een kunststofgranulaat op conventionele spuitgietmachines. Het bindmiddel wordt bij hoge temperatuur gesmolten en de zeer viskeuze massa van metaalpoeder en bindmiddel wordt vervolgens in de matrijs van het desbetreffende bestanddeel gespoten. De resulterende werkstukken van metaalpoeder en bindmiddel worden "groene deel" genoemd en moeten worden omgevormd tot zuiver metalen onderdelen in de volgende processen
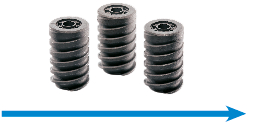
Ontbinden
In de ontbindingsstap wordt het groene deel van het hoofdaandeel aan het bindmiddel onttrokken. Dit gebeurt gewoonlijk door de bindmiddelcomponent op te lossen met een oplosmiddel of door een katalytische reactie. Wat overblijft is een poreus bestanddeel dat bijeengehouden wordt door restbestanddelen van het bindmiddel.
Deze zogenaamde "bruine delen" worden thermisch ontbonden in een oven. Dit betekent dat bij verhoogde temperaturen tussen 400 °C en 900 °C het resterende bindmiddel uit het bestanddeel wordt verdampt. Tegelijkertijd beginnen de metaaldeeltjes zich te binden door zogenaamde sinterhalzen te vormen. Zij geven het bestanddeel voldoende stabiliteit voor de daaropvolgende sinterstap.
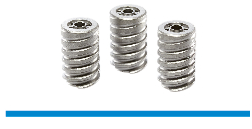
Sinteren
De laatste processtap, het sinteren, sluit de poriën die door het bindmiddel zijn achtergelaten. De componenten worden samengeperst bij hoge temperaturen van meestal meer dan 1.000 °C. Het temperatuurprofiel in de sinteroven is sterk afhankelijk van het materiaal en de geometrie van het onderdeel.
Daarom moet deze processtap zorgvuldig worden aangepast of ontwikkeld voor elke componentgeometrie en elk materiaal – want deze zorg garandeert u de optimale kwaliteit van de componenten gedurende de hele levenscyclus.
FAQ - Veelgestelde vragen en antwoorden over het MIM-proces
Algemene vragen rond MIM
De metaalpoederspuitgiettechnologie (MIM) combineert de ontwerpvrijheid van het kunststofspuitgieten met de voordelen van metalen materialen. Hiermee kunnen complexe metalen onderdelen met hoge precisie en in grote hoeveelheden worden vervaardigd.
MIM maakt de productie mogelijk van filigrane en zeer nauwkeurige componenten met een hoog materiaalgebruik en minimale nabewerking. Het proces is bijzonder rendabel voor de serieproductie van complexe metalen onderdelen.
Verschillende metalen zijn geschikt voor MIM, waaronder roestvrij staal, gereedschapsstaal, titanium en speciale legeringen met hoge sterkte-eigenschappen of corrosiebestendigheid.
Typische toepassingsgebieden zijn de medische technologie, de auto-industrie, lucht- en ruimtevaart, elektronica, de horloge- en juwelenindustrie en industriële toepassingen met hoge eisen aan precisie en materiaaleigenschappen. Over het algemeen worden MIM-onderdelen overal gebruikt waar kleine, complexe metalen onderdelen in grote aantallen nodig zijn.
De fabricagetoleranties liggen meestal bij ±0,5% van de nominale maat, mogelijk zelfs zo laag als 0,3%. Nog nauwkeurigere toleranties kunnen worden bereikt door een gerichte nabewerking van de functionele afmetingen door frezen, draaien, slijpen of polijsten.
MIM is ideaal voor middelgrote tot grote serieproducties. Voor kleinere aantallen bieden we alternatieve productieprocessen zoals CNC-bewerking of additieve productie.
MIM bij de Zimmer Group: Onze sterke punten
Dankzij onze sterk geautomatiseerde productieprocessen kunnen we MIM-onderdelen bijzonder efficiënt en met korte productietijden produceren. Dit maakt snelle levertijden en een rendabele serieproductie mogelijk.
De Zimmer Group verenigt 15 technologische divisies onder één dak. Naast tientallen jaren expertise in handling-, robot-, vacuüm-, dempings-, machine-, klem- en remtechnologie, ontwikkelen we complexe systeemoplossingen zoals specifieke EOAT's (End of Arm Tools) mobiele robotcellen en AMR's (Autonomous Mobile Robots) om flexibel te kunnen reageren op individuele klantvereisten. We maken ook gebruik van 3D-printprocessen om onze klanten optimaal te ondersteunen op het gebied van prototype-ontwikkeling en optimalisatie van onderdelen. Met dit proces kunnen we met behulp van het MEX (Material Extrusion Process) ook metalen, elastomeer- en kunststofonderdelen voor onze klanten vervaardigen.
Dankzij onze eigen gereedschapsmakerij kunnen we snel en flexibel reageren op aanpassingen. Dit verkort de ontwikkelingstijd en bespaart onze klanten externe gereedschapskosten.
We ondersteunen onze klanten tijdens het hele proces – van productontwikkeling, via gereedschapsbouw en spuitgieten tot nabewerking en montage van onderdelen. Dit betekent dat u één aanspreekpunt hebt voor alle productiestappen.
Onze productie is ontworpen om de materiaalefficiëntie te maximaliseren. Het lage materiaalverlies in het MIM-proces, in combinatie met onze grondstofbesparende productiemethode, vermindert het afval en optimaliseert het energieverbruik.
Neem contact met ons op met uw vereisten voor de jaarlijkse hoeveelheid, het materiaal, de mechanische eigenschappen en toleranties van de onderdelen. U kunt ons ook de onderdelentekening en stapgegevens van de onderdelen sturen. Ons team van experts controleert de haalbaarheid en ondersteunt u bij de optimale realisatie van uw componenten.
Aanvraagformulier
Spuitgieten van metaal – MIM
Verwerkingstijd voor aanbiedingen
- Kunststof onderdelen – binnen 3 werkdagen*
- MIM-onderdelen – binnen 3 werkdagen*
- Spuitgietgereedschap (kunststof/MIM) – binnen 3 werkdagen* Gereedschapsaanpassingen – binnen 3 werkdagen*
- Services (frezen, draaien, eroderen) – binnen 3 werkdagen*
*Vereiste: Componentenontwerp is voltooid of vrijgegeven.