Elastomer technology
Flexible right from the start
The Zimmer Group uses state-of-the-art production processes to manufacture sophisticated elastomer components, particularly those with complex geometries. There are no limits to the complexity of the components. We supply practically everything that can be produced using transfer molding (TM) or injection transfer molding (ITM) processes, including inserts such as threaded inserts, springs, and any other parts made of plastic or metal. The Zimmer Group uses state-of-the-art production processes to manufacture sophisticated elastomer components, particularly those with complex geometries. There are no limits to the complexity of the components. We supply practically everything that can be realized using transfer molding (TM) or injection transfer molding (ITM) processes, including inserts such as threaded inserts, springs, and any other parts made of plastic or metal.
OUR KNOW-HOW – your advantage
- Special seals and series seals from a single source
- A wide range of elastomers such as NBR, silicone, EPDM, FPM, CR, TPU, or polyurethane
- All technically possible variations in hardness, coloring, or improved resistance
- Even the most complex geometries can be reproduced
- Flexibility in quantities
- Variability in component sizes
- Development and consulting for process-related geometry optimization
- Installation, assembly, and functional testing
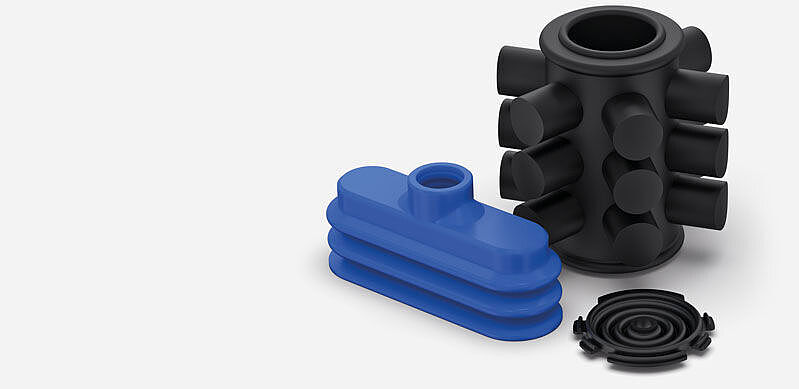
Transfer molding process (TM)
At Zimmer, we use the transfer molding process for single component and small series production of elastomer components. This process involves inserting an uncured rubber mixture into a tool that can be heated. This mixture is cured (vulcanized) and formed into a finished elastomer component.
Injection transfer molding process (ITM)
In contrast to the normal TM process, series production of elastomer components involves subjecting the uncured rubber mixture to an automated injection process, instead of inserting it.
Materials
Nitrile rubber (NBR), silicone, fluororubber (FKM), ethylene propylene diene rubber (EPDM), and polyurethane.
Advantages of elastomer technology at ZIMMER:
- Special seals and series production seals from a single source
- Even the most complex geometries can be reproduced
- Flexibility in terms of quantities: Individual seals, small production series, and large production series can all be manufactured
- Variability in component size: Small, medium-sized, and large components can be produced
- Development of and advice on geometrical optimization in process technology
- Installation, assembly, and functionality testing