MIM technology
METAL INJECTION MOLDING
MIM process
Thanks to the Zimmer Group's metal injection molding process, there are no limits to the production of sophisticated workpieces. Complex shaped series components made of metal often involve a multi-layered production process. The MIM process counteracts this and enables the production of metal parts in almost any shape using injection molding, combining the geometric freedom of plastic injection molding with the strength and wear properties of metals.
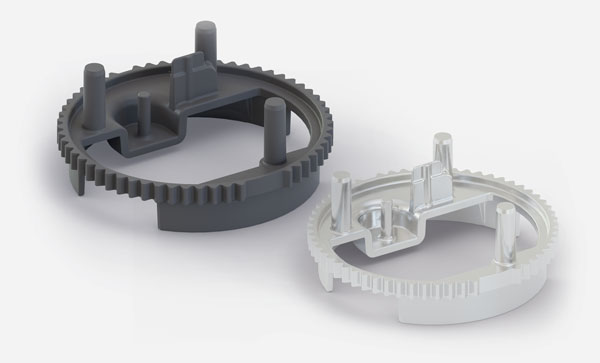
As a result, MIM technology offers you a host of appealing advantages:
- Cost-effective series production of metallic workpieces
- Entirely new level of freedom for designing parts
- Combines the advantages of injection molding technology with the outstanding strength and wear characteristics of metals
- Series production of smaller components with weights from 0.3 g to 150 g
- Complex components with a wall thickness down to 0.2 mm
- Ability to implement small and large holes, inner and outer threading, cross holes, undercuts and gear teeth
- Full utilization of the strength properties of the material being used
- Mechanical strength of workpieces equal to conventional manufacturing processes
- Surface treatment using frictional grinding, mirror polishing, sandblasting, passivation, electropolishing or etching
- Coating using burnishing or plating with chrome, copper, nickel, silver or gold
- Avoids production costs and the use of expensive assembly and connection techniques
- Significantly lower costs for complex components
- 25% to 65% less expensive than conventional production processes
- Applicable in a vast assortment of areas: Gearbox parts, watches, jewelry, eyeglass parts, surgical instruments, tweezers, dental braces, small and micro-sized parts for mobile phones, computers or other devices
MIM The process
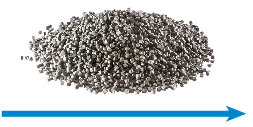
Feedstock
The starting material for metal injection molding is formed from what is known as the feedstock. This consists of about 60% of the respective metal powder by volume and 40% of a binder by volume, i.e. a blend of polymers and waxes. The homogeneous mixture of all of the components is of critical importance, since that is the only way to ensure optimal processing and uniform product quality in later processes.
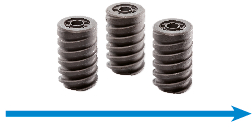
Injection molding
The feedstock is processed using conventional injection molding machines the same way as plastic pellets. The binder portion is melted at a high temperature and the highly viscous mass of metal powder and binder is then pressed into the shape of the respective component. The resulting workpieces made of metal powder and binder are called "green parts" and have to be converted into purely metallic components in the subsequent processes.
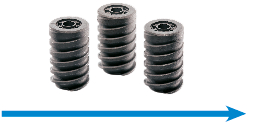
Debinding
In the debinding step, the majority of the binder is removed from the green parts. This normally happens by dissolving the binder components using a solvent or a catalytic reaction. What remains is a porous component held together by the remaining binder. These are then called "brown parts". The remaining binder is then removed in a furnace. This means that the remaining binder is vaporized out of the component at a high temperature between 400 °C and 900 °C. At the same time, the metal particles start to bind together by forming what are known as sinter necks. They give the component sufficient stability for the subsequent sintering step.
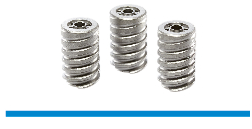
Sintering
The last process step, sintering, closes the pores left over by the binder. The components are compressed at high temperatures, usually over 1,000 °C. The respective temperature profile in the sinter furnace heavily depends on the material and the component geometry. As a result, this process step has to be carefully adapted and developed for each component geometry and each material. It is this care that ensures your components have optimal quality throughout their life cycle.
FAQ - Häufige Fragen und Antworten zum MIM-Verfahren
Allgemeine Fragen rund um MIM
Die Metallpulverspritzguss-Technologie (MIM) kombiniert die Designfreiheit des Kunststoffspritzgusses mit den Vorteilen metallischer Werkstoffe. Damit können komplexe Metallteile in hoher Präzision und großen Stückzahlen gefertigt werden.
MIM ermöglicht die Produktion filigraner und hochpräziser Bauteile mit hoher Materialausnutzung und minimalem Nachbearbeitungsaufwand. Das Verfahren ist besonders kosteneffizient bei der Serienfertigung komplexer Metallkomponenten.
Eine Vielzahl von Metallen ist für MIM geeignet, darunter rostfreie Stähle, Werkzeugstähle, Titan und spezielle Legierungen mit hohen Festigkeitseigenschaften oder Korrosionsbeständigkeit.
Typische Einsatzgebiete sind die Medizintechnik, Automobilindustrie, Luft- und Raumfahrt, Elektronik, Uhren- und Schmuckindustrie sowie industrielle Anwendungen mit hohen Anforderungen an Präzision und Materialeigenschaften. Generell kommen MIM-Teile überall dort zum Einsatz, wo kleine, komplexe Metallteile in großen Stückzahlen benötigt werden.
Die Fertigungstoleranzen liegen typischerweise bei ±0,5 % der Nennmaßgröße ggf. sogar bis zu 0,3 %. Durch gezielte Nachbearbeitung an den Funktionsmaßen durch Fräsen, Drehen, Schleifen oder Polieren lassen sich noch genauere Toleranzen erzielen.
MIM ist ideal für mittlere bis große Serienproduktionen. Für kleinere Stückzahlen bieten wir alternative Fertigungsverfahren wie CNC-Bearbeitung oder additive Fertigung an.
MIM bei der Zimmer Group: Unsere Stärken
Dank unserer hochautomatisierten Fertigungsprozesse können wir MIM-Bauteile besonders effizient und mit kurzen Produktionszeiten herstellen. Dies ermöglicht schnelle Lieferzeiten und eine kosteneffiziente Serienproduktion.
Die Zimmer Group vereint 15 Technologiebereiche unter einem Dach. Neben jahrzehntelangem Know-how in Handhabungs-, Roboter-, Vakuum-, Dämpfungs-, Maschinen-, Klemm- und Bremstechnik entwickeln wir komplexe Systemlösungen, wie spezifische EOATs (End of Arm Tools) mobile Roboterzellen und AMRs (Autonome Mobile Roboter), um flexibel auf individuelle Kundenanforderungen reagieren zu können. Darüber hinaus setzen wir auf 3D-Druckverfahren, um unsere Kunden im Bereich Prototypenentwicklung oder Baugruppenoptimierung optimal unterstützen zu können. In diesem Verfahren können wir über das MEX (Material Extrusion Verfahren) auch Metall-, Elastomer- und Kunststoffteile für unsere Kunden fertigen.
Durch unseren internen Werkzeugbau können wir schnell und flexibel auf Anpassungen reagieren. Dies reduziert die Entwicklungszeiten und spart unseren Kunden externe Werkzeugkosten.
Wir begleiten unsere Kunden durch den gesamten Prozess – von der Produktentwicklung über den Werkzeugbau und Spritzguss bis hin zur Nachbearbeitung und Baugruppenmontage. So haben Sie einen einzigen Ansprechpartner für alle Fertigungsschritte.
Unsere Fertigung ist auf maximale Materialeffizienz ausgelegt. Der geringe Materialverlust beim MIM-Verfahren, gepaart mit unserem ressourcenschonenden Produktionsansatz, reduziert Abfall und optimiert den Energieverbrauch.
Kontaktieren Sie uns mit Ihren Anforderungen zur Jahresmenge, Material, mechanischen Eigenschaften sowie Toleranzen der Teile. Sie können uns auch die Teilezeichnung und Step-Daten der Bauteile schicken. Unser Expertenteam prüft die Machbarkeit und unterstützt Sie bei der optimalen Umsetzung Ihrer Bauteile.
Request form
Metal injection molding - MIM
Times for offer - market requirements
- Plastic parts - within 3 working days*
- MIM parts - within 3 working days*
- Injection moulding tools (plastic/MIM) - within 3 working days*
- Tool changes - within 3 working days*
- Services (milling, turning, eroding) - within 3 working days*
*Prerequisite: Component design is completed or released.