Tecnología MIM
METAL INJECTION MOLDING
PROCESO MIM
Gracias al proceso Metal Injection Moulding de Zimmer Group, no hay límites para la producción de piezas de trabajo sofisticadas. Los componentes de serie de formas complejas fabricados en metal suelen ir acompañados de un esfuerzo de producción de varios niveles. El proceso MIM contrarresta esta situación y permite fabricar piezas metálicas de casi cualquier forma mediante el moldeo por inyección, combinando la libertad geométrica del moldeo por inyección de plástico con la resistencia y las propiedades de desgaste de los metales.
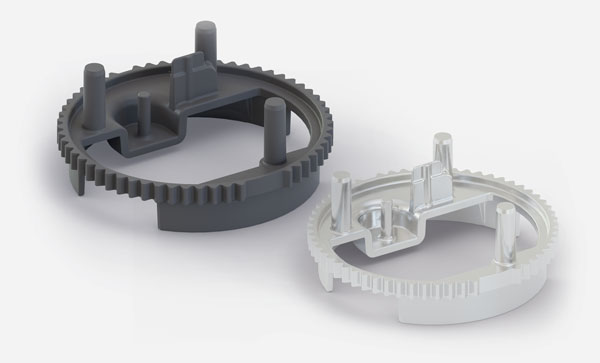
La tecnología MIM le ofrece muchas ventajas convincentes:
- Producción en serie económica de componentes metálicos complejos
- Libertad de diseño en el desarrollo de sus componentes y grupos constructivos
- Libertad de materiales: aceros inoxidables, aceros de baja aleación, aceros HSS, así como metales duros, titanio y aleaciones de titanio y metales pesados
- Producción en serie de componentes con pesos de 0,3 g a 150 g de peso de la pieza
- Se pueden realizar componentes complejos con espesores de pared de hasta 0,2 mm
- Taladros, roscas interiores y exteriores, destalonamientos y dentados
- Resistencia mecánica y capacidad de mecanizado, como en piezas de trabajo fabricadas de forma convencional
- Tratamiento de superficies mediante rectificado, abrillantado, tratamiento con chorro de arena, pasivación, electropulido o decapado
- Recubrimiento mediante pavonado, cromado, cobreado, niquelado, baño de plata o dorado
- Evita costes de producción gracias al ahorro de la costosa técnica de montaje y unión
- En geometrías de componentes complejas aprox. 25 %-65 % más económico que los procesos de producción convencionales
- Los campos de aplicación se encuentran allí donde se utilizan componentes metálicos en serie pequeños y complejos, por ejemplo, en piezas de engranajes, en la industria relojera, joyera y de gafas, en componentes de la técnica médica, en componentes de ingeniería mecánica y manipulación, en piezas pequeñas para teléfonos móviles, ordenadores y otros dispositivos.
CONTACTO
MIM - El proceso
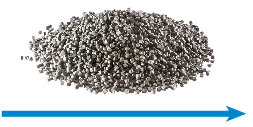
Materia prima
El material de partida para el moldeo por inyección de polvo metálico es la denominada «materia prima». Consiste en aproximadamente un 60 % en volumen del polvo metálico correspondiente y un 40 % en volumen de un aglutinante, es decir, una mezcla de polímeros y ceras. La mezcla homogénea de todos los componentes es de vital importancia, ya que es la única forma de garantizar un procesamiento óptimo y una calidad constante del producto en el proceso posterior.
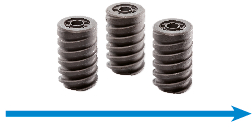
Moldeo por inyección
La materia prima se procesa del mismo modo que el granulado de plástico en las máquinas de moldeo por inyección convencionales. El componente aglutinante se funde a una temperatura elevada y, a continuación, la masa altamente viscosa de polvo metálico y aglutinante se inyecta en el molde del componente correspondiente. Las piezas de trabajo resultantes de polvo metálico y aglutinante se denominan «pieza verde» y deben convertirse en componentes puramente metálicos en los procesos posteriores.
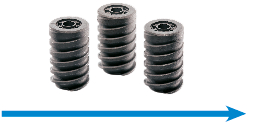
Desbanderizado
En el paso de desbanderizado, la parte principal del aglutinante se separa de la pieza verde. Esto se hace normalmente disolviendo el componente aglutinante con disolventes o mediante una reacción catalítica. Lo que queda es un componente poroso que se mantiene unido por componentes residuales del aglutinante.
Estas denominadas «piezas marrones» se eliminan térmicamente en un horno. Esto significa que el desbanderizado restante se evapora del componente a una temperatura elevada de entre 400 °C y 900 °C. Al mismo tiempo, las partículas metálicas comienzan a unirse formando los denominados cuellos de sinterizado. Estos confieren al componente la estabilidad suficiente para la posterior etapa de sinterizado.
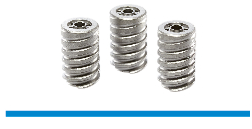
Sinterizado
El último paso del proceso, el sinterizado, cierra los poros dejados por el aglutinante. Los componentes se compactan a altas temperaturas, normalmente superiores a 1000 °C. El perfil de temperatura correspondiente en el horno de sinterizado depende en gran medida del material y de la geometría del componente.
Por este motivo, este paso del proceso debe adaptarse o desarrollarse cuidadosamente para cada geometría de componente y cada material, ya que este cuidado le garantiza la calidad óptima de los componentes durante todo el ciclo de vida.
FAQ - Preguntas y respuestas frecuentes sobre el proceso MIM
Preguntas generales sobre el proceso MIM
La tecnología de inyección de polvo metálico (MIM) combina la libertad de diseño de la tecnología de inyección de plásticos con las ventajas de los materiales metálicos. Esto permite fabricar piezas metálicas complejas con gran precisión y en grandes cantidades.
El proceso MIM permite fabricar componentes muy delicados y de alta precisión con un elevado aprovechamiento del material y un mínimo esfuerzo de postmecanizado. El proceso es especialmente rentable para la producción en serie de componentes metálicos complejos.
Hay una gran variedad de metales adecuados para MIM, como aceros inoxidables, aceros para herramientas, titanio y aleaciones especiales con propiedades de alta resistencia o resistencia a la corrosión.
Los campos de aplicación típicos son la técnica médica, la industria automovilística, la industria aeroespacial, la electrónica, la industria relojera y joyera y aplicaciones industriales con elevados requisitos de precisión y propiedades de los materiales. En general, las piezas MIM se utilizan siempre que se necesitan piezas metálicas pequeñas y complejas en grandes cantidades.
Las tolerancias de fabricación suelen ser del ±0,5 % del tamaño nominal, e incluso del 0,3 %. Se pueden conseguir tolerancias aún más precisas mediante un postmecanizado selectivo de las dimensiones funcionales mediante fresado, torneado, rectificado o pulido.
El proceso MIM es ideal para la producción de series medianas y grandes. Para cantidades menores, ofrecemos procesos de fabricación alternativos, como el mecanizado CNC o la fabricación aditiva.
MIM en Zimmer Group: Nuestros puntos fuertes
Gracias a nuestros procesos de producción altamente automatizados, podemos fabricar componentes MIM con especial eficacia y en plazos de producción cortos. Esto permite plazos de entrega rápidos y una producción en serie rentable.
Zimmer Group reúne 15 ámbitos tecnológicos bajo un mismo techo. Además de los conocimientos especializados acumulados a lo largo de muchas décadas en tecnología de manipulación, de robots, vacío, amortiguación, máquinas, sujeción y frenado, desarrollamos soluciones de sistema complejas como celdas de robot móviles EOAT (End of Arm Tools) específicas y AMR (Autonomous Mobile Robots) para poder reaccionar con flexibilidad a las necesidades individuales de los clientes. También utilizamos procesos de impresión 3D para ofrecer a nuestros clientes un apoyo óptimo en las áreas de desarrollo de prototipos y optimización de componentes. Mediante este proceso, también podemos fabricar piezas de metal, elastómero y plástico para nuestros clientes utilizando el proceso MEX (proceso de extrusión de material).
Gracias a nuestro departamento interno de fabricación de herramientas, podemos reaccionar con rapidez y flexibilidad a las adaptaciones. Esto reduce los tiempos de desarrollo y ahorra a nuestros clientes costes externos en herramientas.
Acompañamos a nuestros clientes a lo largo de todo el proceso, desde el desarrollo del producto, la fabricación de herramientas y el moldeo por inyección hasta el postmecanizado y el montaje de los componentes. De este modo, dispondrá de un único punto de contacto para todas las fases de producción.
Nuestra producción está diseñada para maximizar la eficiencia de los materiales. La escasa pérdida de material en el proceso MIM, unida a nuestro enfoque de producción que ahorra recursos, reduce los residuos y optimiza el consumo de energía.
Póngase en contacto con nosotros e infórmenos de sus requisitos en cuanto a la cantidad anual, el material, las propiedades mecánicas y las tolerancias de las piezas. También puede enviarnos un dibujo de la pieza y los datos técnicos de los componentes. Nuestro equipo de expertos comprobará la viabilidad y le ayudará para una implementación óptima de sus componentes.
Formulario de solicitud
Metal injection molding - MIM
Tiempo de tramitación de las ofertas
- Piezas de plástico - en el plazo de 3 días laborables*
- Piezas MIM - en el plazo de 3 días laborables*
- Herramientas de moldeo por inyección (plástico/MIM) - en el plazo de 3 días laborables*
- Modificaciones de herramientas - en el plazo de 3 días laborables*
- Servicios (fresado, torneado, erosión) - en el plazo de 3 días laborables*
*Requisito previo: la construcción de los componentes debe haber finalizado o haberse aprobado.