Innovations from the Zimmer Group
Innovations from our technology areas
NEW PRODUCT PORTFOLIO
VACUUM TECHNOLOGY
GRIPPING SOLUTIONS THAT HOLD SECURELY!
With our variety of vacuum components, we have the right solution for all of your applications. From individualcomponents to comprehensive all-in-one systems. Our product portfolio includes everything from simple vacuum suction cups and complex gripper systems to modular quick-change systems such as Smart Cup and Magic Cup. Modular quick-change systems enable uncomplicated customization, while all-in-one solutions offer seamless integration into existing production processes.
This means that vacuum applications can be optimally tailored to your individual requirements, guaranteeing maximum flexibility and efficiency. You can also use the product configurator to find the perfect solution for your requirements.
COMPREHENSIVE PRODUCT RANGE OUR EXPERTISE – YOUR ADVANTAGE
- Maximum efficiency: Using our advanced technologies, you can accelerate your processes and increase your productivity.
- Extraordinary precision: Our products guarantee precise handling and processing, which are essential for demanding tasks.
- Reliability: High-quality materials and innovative engineering ensure a long service life and low maintenance work.
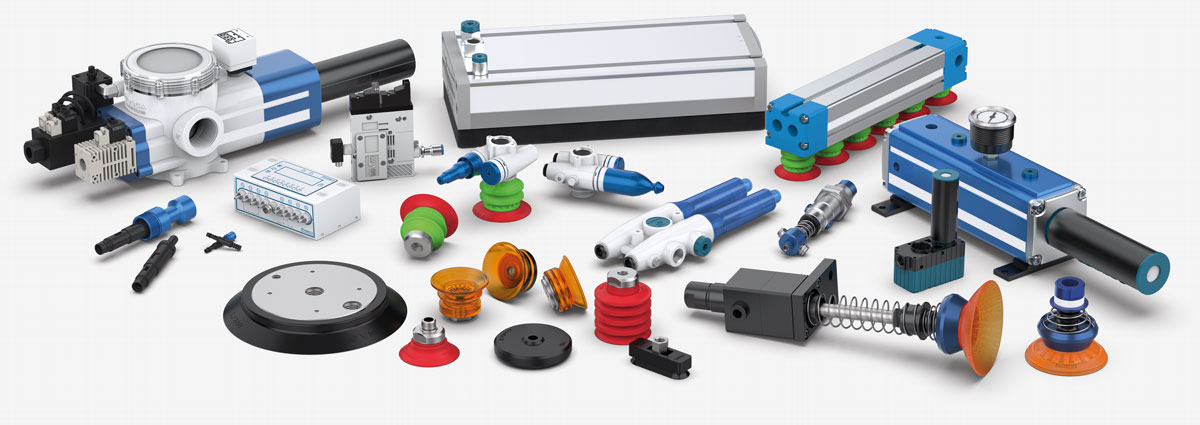
NEW LONG-STROKE AXES
AMB AND AMS SERIES
EXPANDED PORTFOLIO
Compact axes and long-stroke axes are key elements of modern automation technology – precise, efficient and versatile. We are expanding our existing portfolio of compact axes from the AC series with our long-stroke axes from the AMB and AMS series in order to optimally meet requirements for longer travel paths. The toothed-belt axes of the AMB series stand for high dynamics, speed and range – ideal for short cycle times. The spindle axes of the AMS series are characterized by excellent precision and high feed forces and are therefore predestined for applications where the focus is on both load capacity and accuracy.
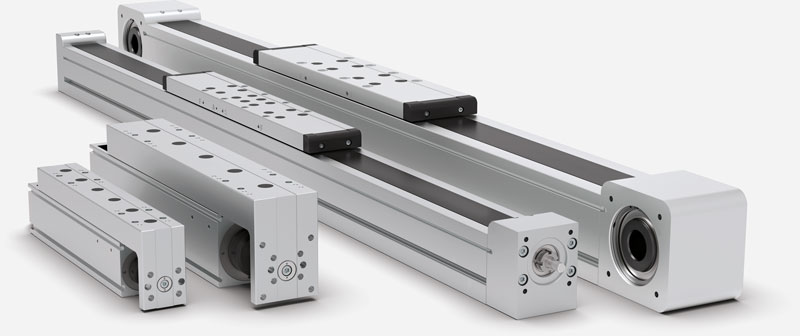
Long-stroke axes with a toothed belt drive | ||||
---|---|---|---|---|
Installation size | Max. stroke [mm] | Max. speed [m/s] | Max. acceleration [m/s²] | Max. holding force [N] |
AMB040 | 1.810 | 4 | 50 | - |
AMB060 | 5.670 | 5 | 50 | 400 |
AMB080 | 5.610 | 5 | 50 | 650 |
AMB120 | 5.550 | 5 | 50 | 1.200 |
Long-stroke axes with a spindle drive | ||||
---|---|---|---|---|
Installation size | Max. stroke [mm] | Max. speed [m/s] | Max. acceleration [m/s²] | Max. holding force [N] |
AMS040 | 900 | 0,5 | 30 | - |
AMS060 | 1.970 | 1,5 | 30 | 250 |
AMS080 | 2.100 | 2 | 30 | 500 |
AMS120 | 2.300 | 3,2 | 30 | 1.000 |
NEW GRIPPER WITH ROTARY MODULE
REP2000 SERIES
TWO IN ONE
The new 2-jaw parallel rotary gripper from the REP2000 series combines gripping and turning in one compact module, setting new standards in terms of efficiency and space savings. The system enables optimum use of the available installation space and offers maximum functionality in a robust design. With protection class IP40 or IP54, the parallel rotary gripper is also ideally suited for harsh industrial environments.
Control via IO-Link allows you to flexibly adapt the stroke of the gripper jaws to the workpiece and adjust the approach angle of the endlessly rotating unit to the application.
OUR EXPERTISE – YOUR ADVANTAGE
- 5 million maintenance-free cycles
- Positionability via IO-Link
- Mechanical self-locking mechanism
- Adjustable swivel angle
- IP40 or IP54
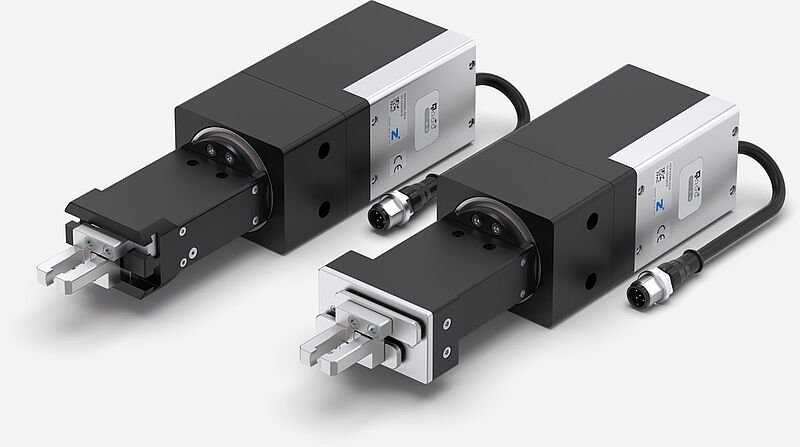
NEW ASEPTIC TOOL CHANGER
WMR2000 SERIES
ASEPTIC STANDARD PRODUCT FOR SPECIAL REQUIREMENTS
The aseptic tool changer from the WMR2000 series features a hygienic, FDA-compliant design and meets the requirements of protection class IP68. The housing is made of easy-to-clean PET and is hydrogen peroxide resistant, making it ideal for use in hygienically sensitive areas. Up to four pneumatic pass throughs are supported. The innovative use of materials means that it is extremely light and compact.
The magnetic tool changer enables the fast and easy exchange of tools. A permanent electromagnet ensures that the tool and workpiece remain connected reliably, even when the electricity fails – a key safety feature. Match it with the aseptic pharmaceutical gripper based on the GEP2000 and GEH6000 series. The customized grippers with a hygienic design meet the highest hygiene and cleaning requirements and are ideal for use in sensitive applications and clean rooms.
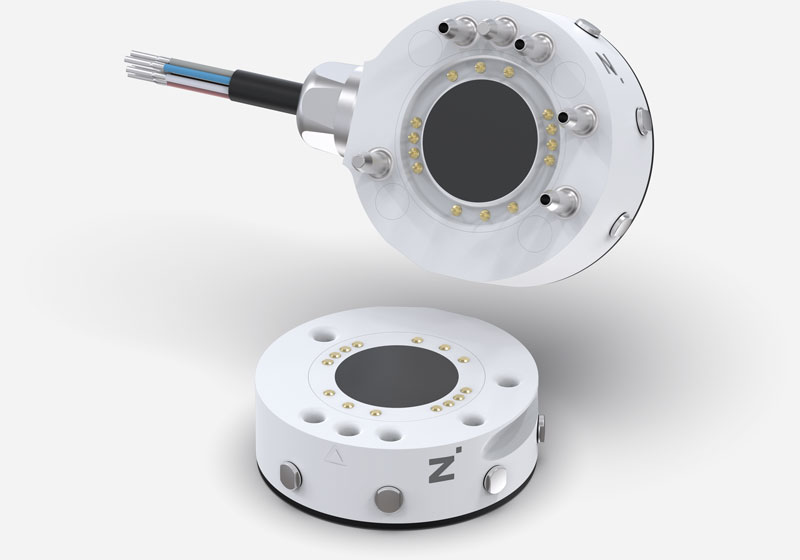
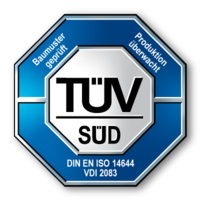
Tool changer
WPR5000 series
NEW TOOL CHANGER SERIES FOR ALL INDUSTRIES
The new WPR5000 tool changer series is characterized by a flat design and, depending on the installation size and application, can carry high payloads of over 500 kg. The tool changer has been specially developed for demanding applications where high repeatability and maximum service life are essential. The WPR5000 offers maximum flexibility for a wide range of applications thanks to the wide variety of installation sizes. Up to ten integrated pneumatic pass through ports ensure reliable compressed air and vacuum transmission with large cross-sections, while an endless variety of other energy elements can be optionally selected for other requirements (load current, signal current, hydraulics and communication).

NEW ENERGY ELEMENTS
WER1500, WER3000 AND WER4000 SERIES
ENDLESS VARIETY
Energy elements are the most important accessories for tool changers and are essential for the transmission of a wide range of different media from the stationary part to the loose part. All tool changers offer integrated air transfer systems as standard. If larger or smaller cross-sections are needed, energy elements can be used. In addition, almost all media such as load current, signal current, hydraulics and communication can be transmitted using energy elements.
OUR EXPERTISE – YOUR ADVANTAGE
- Standardized: Standardized interfaces and a modular design ensure flexible and cost-effective integration into all applications.
- Integration: Components can be integrated seamlessly into existing systems and processes.
- Innovative: The most modern technologies for efficient and future-proof solutions.
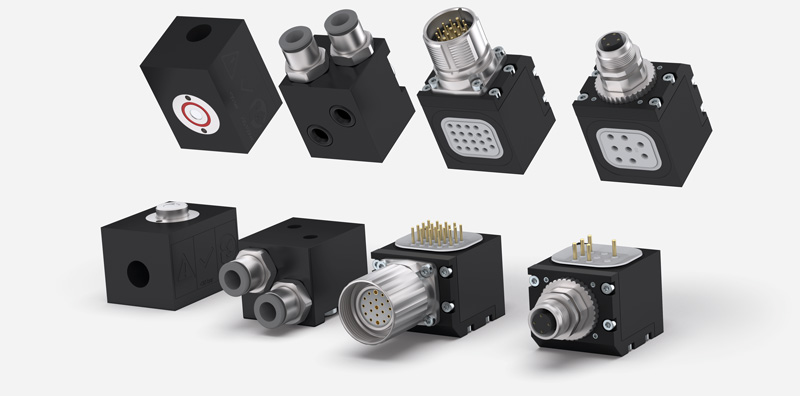
NEW HEAVY-DUTY AXIS COMPENSATION MODULES
XYR9000, ZR9000, CR9000 Series
PRECISION MEETS ROBUSTNESS
With the new heavy-duty axis compensation modules from the XYR9000, ZR9000 and CR9000 series the Zimmer Group sets new benchmarks in industrial automation. Conventional systems quickly reach their limits, especially when handling heavy workpieces. This is precisely where the new heavy-duty axle compensation modules come into play. They offer exceptionalrobustness for loads from 500 kg up to 2,000 kg, without compromising on precision and flexibility. The series enable axis compensation in the X, Y and Z directions as well as rotational compensation movements. A special highlight is the ability to combine axis compensation modules of the same size for maximum adaptability to a wide range of requirements.
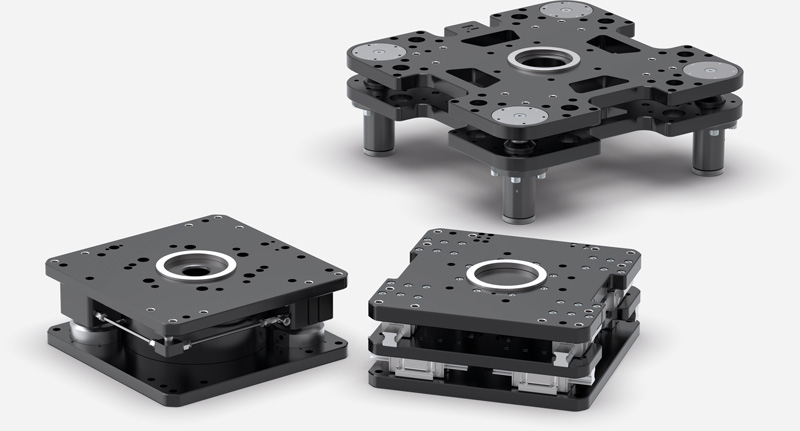
XYR9000 series | ||||
---|---|---|---|---|
Installation size | Stroke X/Y level +/- [mm] | Centered holding force [N] | Weight [kg] | IP class |
XYR9050 | 15,0 | 10000 | 37 - 40 | IP 40 |
XYR9075 | 15,0 | 10000 | 61 - 63 | IP 40 |
XYR9100 | 20,0 | 20000 | 89 - 93 | IP 40 |
XYR9150 | 20,0 | 20000 | 110 - 120 | IP 40 |
XYR9200 | 20,0 | 20000 | 140 - 150 | IP 40 |
NEW ANGLE FLANGE
FOR THE MATCH END-OF-ARM ECOSYSTEM
FROM PICK & PLACE TO MACHINE LOADING
The angle flange of the LWR series was developed specifically for the MATCH end-of-arm ecosystem and enables quick and tool-free changes within seconds. It can be used universally, fits all common robot models and combines the two main handling technologies: Gripping and vacuum systems. Integration is particularly simple and direct – especially for IO-Link-capable grippers from the GEP2000, GEP5000, GEH6000IL and GPD5000IL series. Thanks to its compact design, the angle flange ensures a small interference contour and thus maximum freedom of movement. The compressed air supply and IO-Link control are integrated directly in the flange, which minimizes the installation effort. The flange is optionally available with a blow-out nozzle and a programming tip to extend the functionality even further.
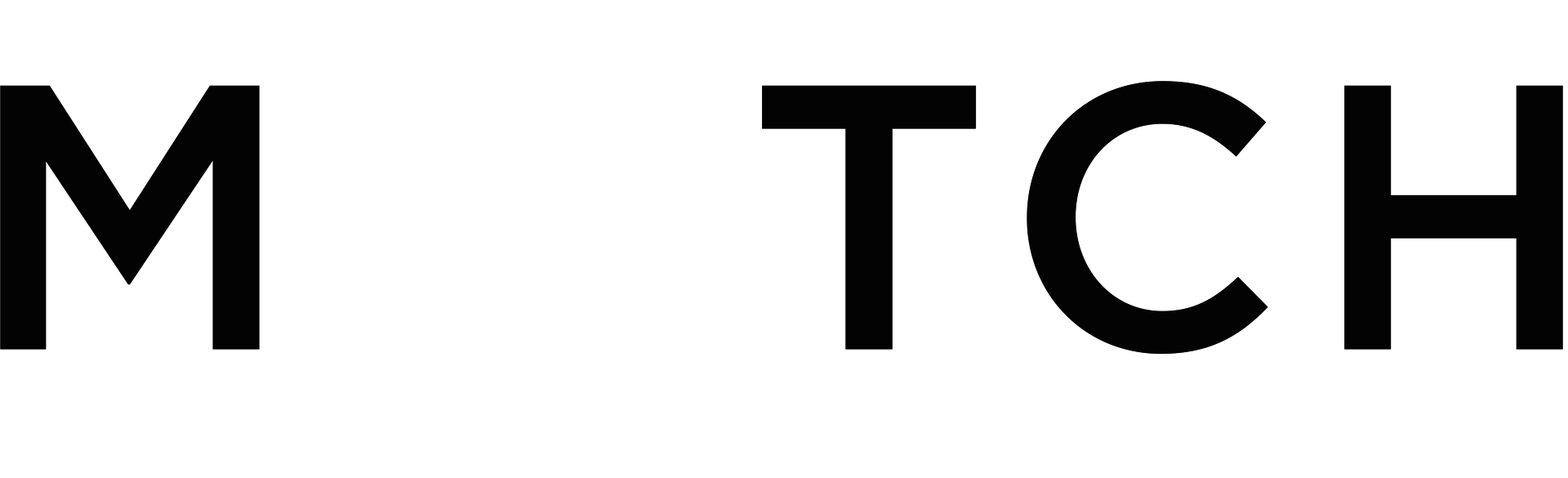
ZIMO AUTOMATION CELL
FOR BEGINNERS AND EXPERTS
THE ROBOT CELL FOR ANY REQUIREMENT
ZiMo is the mobile and cost-effective process automation solution for companies of all sizes. The modular system and versatile accessories make it easy to put together a customized, flexibly adaptable package – perfect for beginners and experienced programmers alike.
Easy Automation – easy integration
With Easy Automation, you get an all-round carefree package. The Zimmer HMI gives you easy control of the system, including the option of complete integration and commissioning. At the same time, you benefit from the wide range of options and accessories.
Platform Kit – configurable as you like
Would you like to program ZiMo completely by yourself? With the Platform Kit, you get the basic module with or without PLC and all ZiMo options and can configure the robot cell entirely according to your requirements.
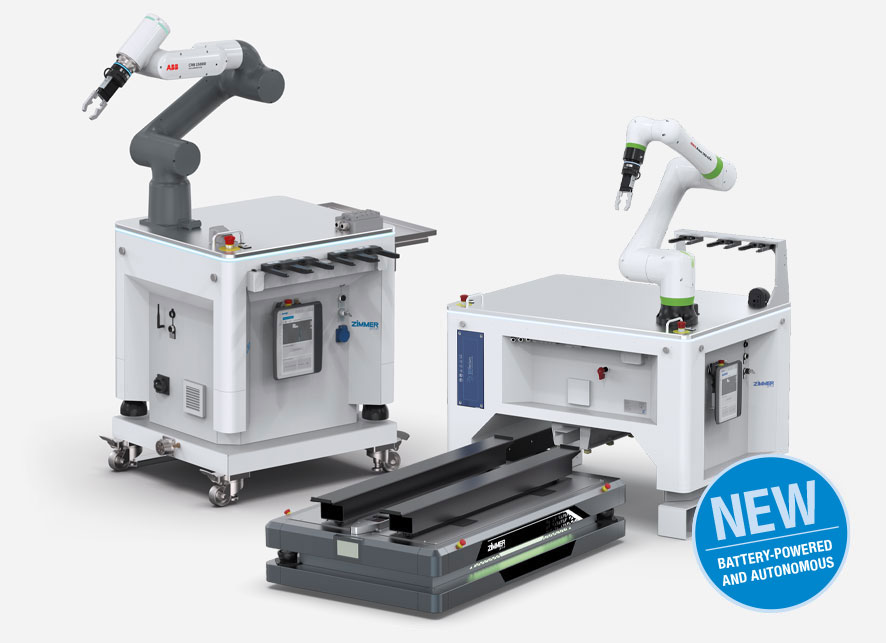
MILES
AUTONOMOUS MOBILE ROBOT
INDIVIDUAL, DRIVERLESS TRANSPORT SYSTEMS FOR PRODUCTION AND LOGISTICS PROCESSES
In recent years, autonomous mobile robots (AMRs) have developed into a revolutionary force that has transformed industries and redefined efficiency in many different sectors. AMRs are intelligent, self-navigating machines
that are designed to perform tasks without direct human intervention.
They combine state-of-the-art technologies and modern sensors to navigate complex environments, interact with objects and perform tasks with precision.
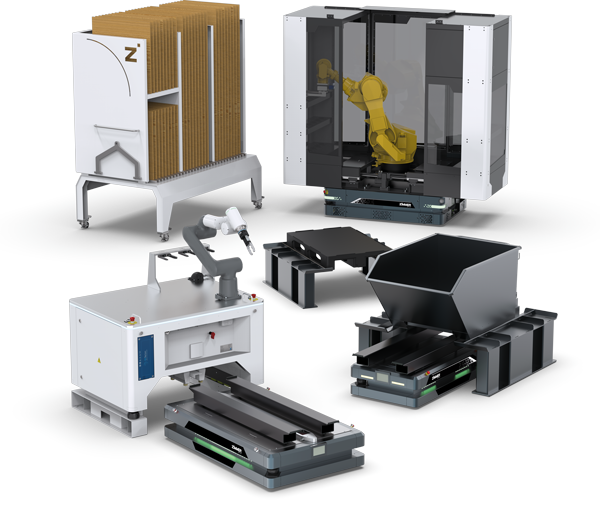
OUR EXPERTISE – YOUR ADVANTAGES
Maximum availability
- Best view of the work area at all times
- Collaborative cooperation – human and machine in one system
Modular concept with free layout design
- No need for protective housing
- Interface for setting up different modules possible
- Subsequent integration into existing processes possible
Simple extension of the automation system
- Additional AMRs can be integrated into the system later
Complete system comprising hardware, software and servicing
- Complete integration into the entire production process, with control architecture from a single source
- Comprehensive system overview with powerful master computer
- Intelligent navigation and fleet management: Reprogramming of the AMR travel paths possible at any time
MOSAIC
MODULAR AUTOMATION PLATFORM
COMPREHENSIVE MODULARITY
MOSAIC (Modular System of Automation, Information and Communication) is a scalable, modular platform for the intelligent control and networking of technical systems in production and logistics. It combines modern automation and communication technologies with powerful data processing and is the basis for flexible, end-to-end processes.
Numerous functional units enable seamless integration into existing structures. Interfaces to MES and ERP systems allow direct ordering and order tracking. Fleet management coordinates autonomous mobile robots (AMRs) and modular transport control systems efficiently regulate the material flow.
For warehouse logistics, strategies for storage, retrieval and space allocation are available. Stacking logistics make it easy to stack and unstack all sorts of materials with lots of flexibility. Modules for simulation and optimizationgive you help develop logistics, calculate cycle times and improve processes.
Vision and sensor systems recognize objects, conditions and quality features. With the periphery connections,
you can integrate external components such as doors, gates, machines or building technology. This makes MOSAIC a holistic solution for state-of-the-art networked automation and logistics environments.
NEW ZERO-POINT CLAMPING SYSTEM
SPN SERIES WITH ELECTRICAL SENSING
SPN SERIES
The new "ED" version of the SPN series zero-point clamping system enables electrical status monitoring for the open and clamped clamping states as well as component presence sensing. It is an important function for automated production processes in which process reliability and real-time monitoring are of crucial. Other standard functions are opening, the PLUS connection and blowing out.
All clamping systems from the Zimmer Group have form-fit locking by means of clamping segments adapted to the bolt contour, which ensures an extremely rigid connection that can withstand the highest forces and guarantees maximum repeat accuracy.
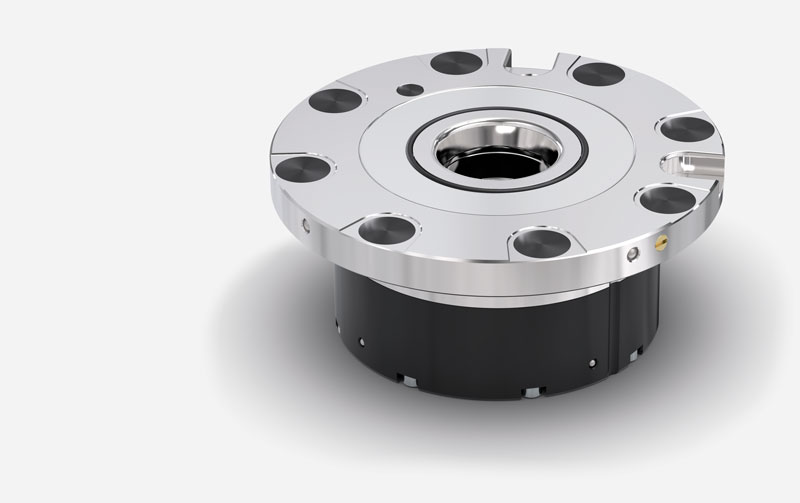
SPN series | Technical data | ||||
---|---|---|---|---|---|
Order No. | SPN062ED | SPN112ED | SPN138ED | ||
Operating pressure [bar] | 4 - 7 | 4 - 7 | 4 - 7 | ||
Clamping force [kN] | 1 - 2 | 4 - 6 | 12 - 18 | ||
Clamping force with PLUS connection [kN] | 2,5 - 5 | 10 - 15 | 24 - 36 | ||
Piston position sensing / positioning check | Electric | Electric | Electric |
NEW MOTOR SPINDLES
ADAPTED TO CUSTOMER REQUIREMENTS
CUSTOMIZED SOLUTIONS
The Zimmer Group is a manufacturer of high-quality motor spindles that, together with matching accessories and peripherals give you everything you need for maximum precision and performance in your production. Our portfolio includes not only a wide selection of standard motor spindles, but also the development of individual, customized solutions that are perfectly tailored to your specific requirements. Our great strength lies in our ability to develop innovative and flexible solutions that not only meet the highest technological standards, but also significantly increase the efficiency and productivity of your applications.
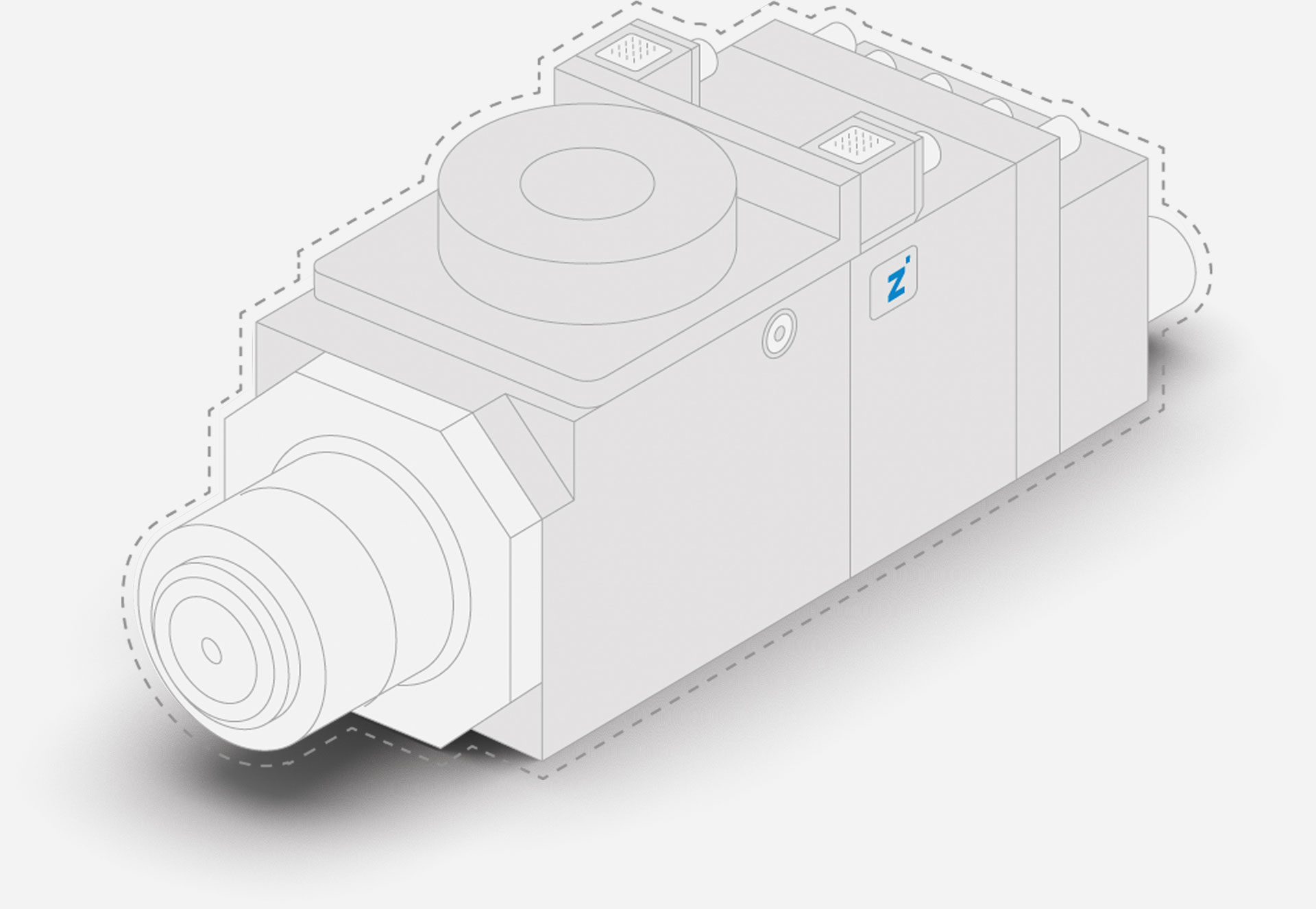
- Smart process control or diagnostics through IO-Link
- Sensors for temperature, speed & vibrations
- Rotary feed-through for MQL & IKZ
- Controllable connections
- Smart process control or diagnostics through IO-Link
- Sensors for temperature, speed & vibrations
- Rotary feed-through for MQL & IKZ
- Controllable connections
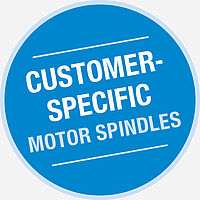
NEW MOTOR SPINDLES
ELECTRIC DEBURRING SPINDLE
ELECTRIC MOTOR SPINDLE FOR DEBURRING
Using robots to deburr parts is becoming more important and is turning into a key technology for a lot of industries. To meet the growing demand, the Zimmer Group develops customized electrical solutions that are specially tailored to the requirements of modern deburring. With our innovative systems, a wide range of components and materials can be processed efficiently and precisely – and with a huge selection of tools.
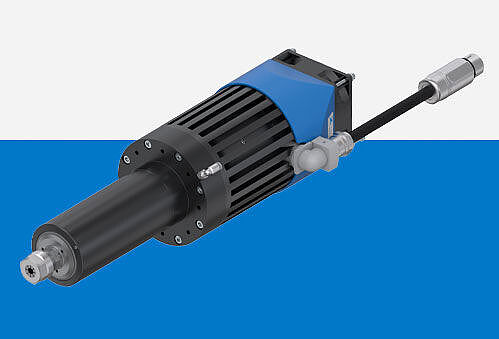
Without deflection

Rigid motor spindle without deflection function of the spindle shaft.
+ Air-cooled
+ Manual tool change
+ Automatic tool change
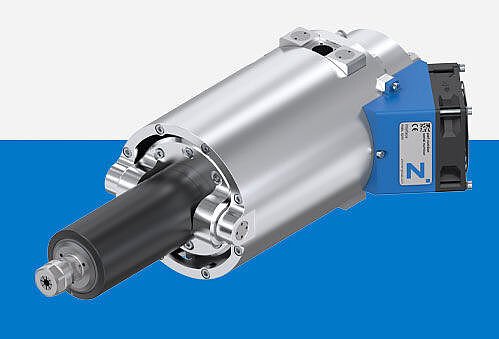
Radial deflection

Radial deflection function of the spindle shaft with lockable degrees of freedom. Optionally available with damping module for even better machining results.
+ Air-cooled
+ Manual tool change
+ Automatic tool change
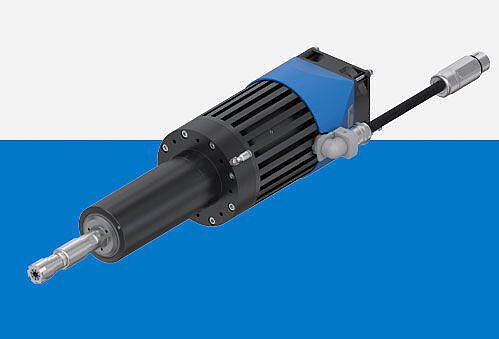
Axial deflection

Motor spindle with axial deflection function of the spindle shaft.
+ Air-cooled
+ Automatic tool change
NEW MACHINING ROBOT
RapTor
RAPTOR MACHINING ROBOT
Raptor, the heart of the machining cell, was specially developed for the woodworking industry and carries out precise cutting, shaping, sanding and lacquering tasks. Its use helps to increase efficiency and reduce costs, as it completes complex tasks quickly, precisely and in a more space-saving manner than portal machines. Raptor has a multi-functional head with 2 flanges, a change interface for quick tool changes and will impress you with its internal energy supply system.
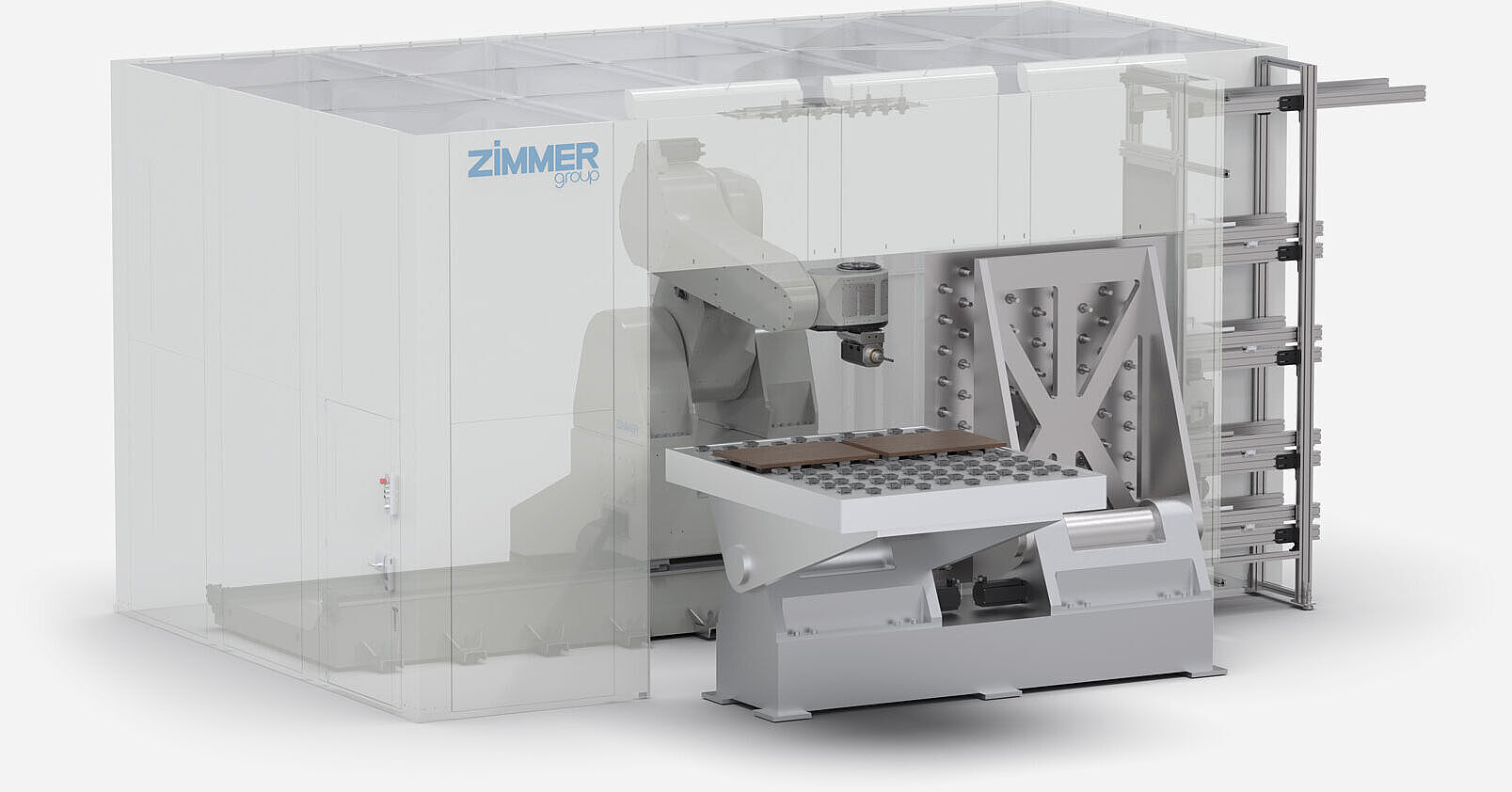
MOBILE ROBOTICS
ZRM SERIES
ZRM SEIRES – ROBOT TRAVERSING AXIS
The robot traversing axis from the ZRM series is required when robots have to travel in parallel on production lines or load multiple machines. The ZRM series is designed for 4 sizes of robots and offers load capacities of up to 2,500 kg per carriage. Thanks to modular segments, different run lengths can be implemented flexibly. Optional extras include weld-proof covers, secure clamping of the carriage position and an additional carriage for using two robots on a 7th axis to complete to offer.
OUR EXPERTISE – YOUR ADVANTAGE
- Robust
- Flexible
- Durable
- Customized
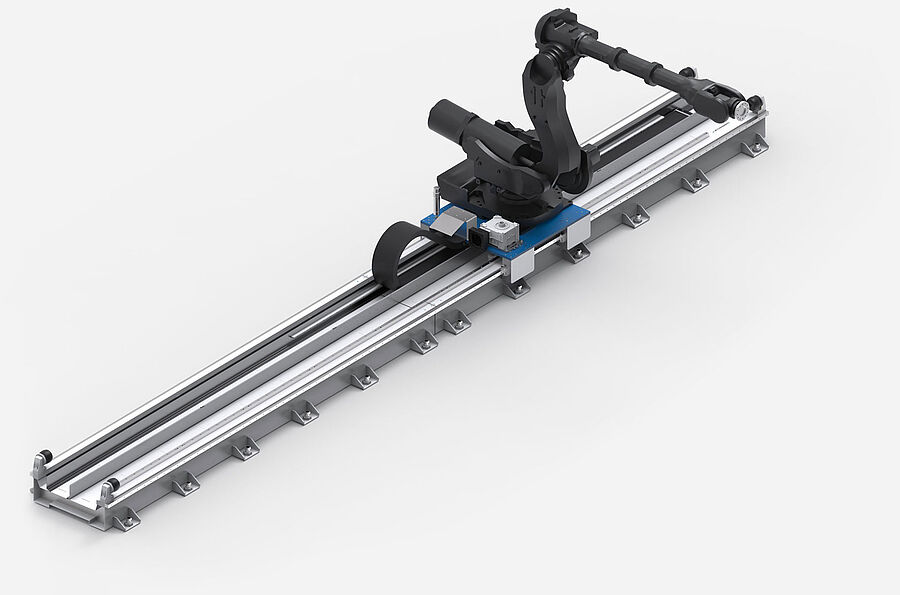
ZRM SERIES | Technical data | ||||
---|---|---|---|---|---|
Order No. | ZRM 250 | ZRM 1000 | ZRM 1500 | ZRM 2500 | |
Max. load capacity [kg] | 250 | 1000 | 1500 | 2500 | |
Total length min. / max: [mm] | 2.000… 100.000 | 2.000… 100.000 | 3.500… 100.000 | 3.500… 100.000 | |
Positioning repeat accuracy [mm] | +/- 0,05 | +/- 0,05 | +/- 0,05 | +/- 0,05 | |
Max. acceleration [m/s2] | 4 | 4 | 4 | 3 | |
Max. speed [m/s] | 1,6 | 1,6 | 1,5 | 1,5 |
MOBILE ROBOTICS AND TRANSPORT SYSTEMS
systems
TAILOR-MADE CONVEYOR LINES
We develop customized, scalable transport systems and conveyor lines across industries that can be seamlessly integrated into your production system. Our complete solutions include conveyor systems such as roller conveyors, belt conveyors, strap conveyors and angled transfer units, all with outstanding adaptability and flexibility.
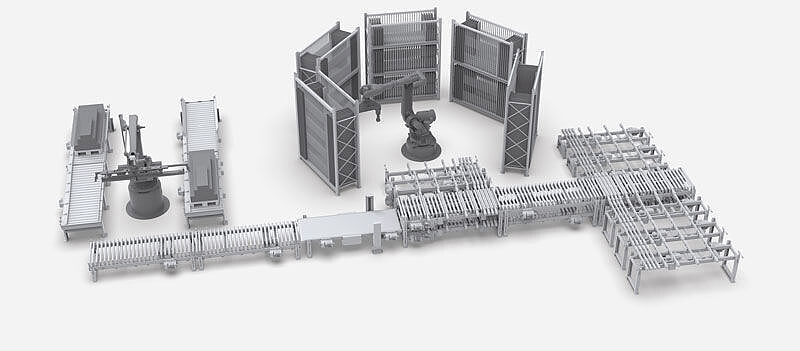
MACHINERY AND CELLS
Systeme
Logistics solutions: Sorting and decoupling cells
This logistics system enables the automatic storage of manually stacked parts as well as the identification and control of the workpieces on the central conveyor belt. The parts are distributed efficiently across three identical storage cells to balance the load before being transported to the next process step.
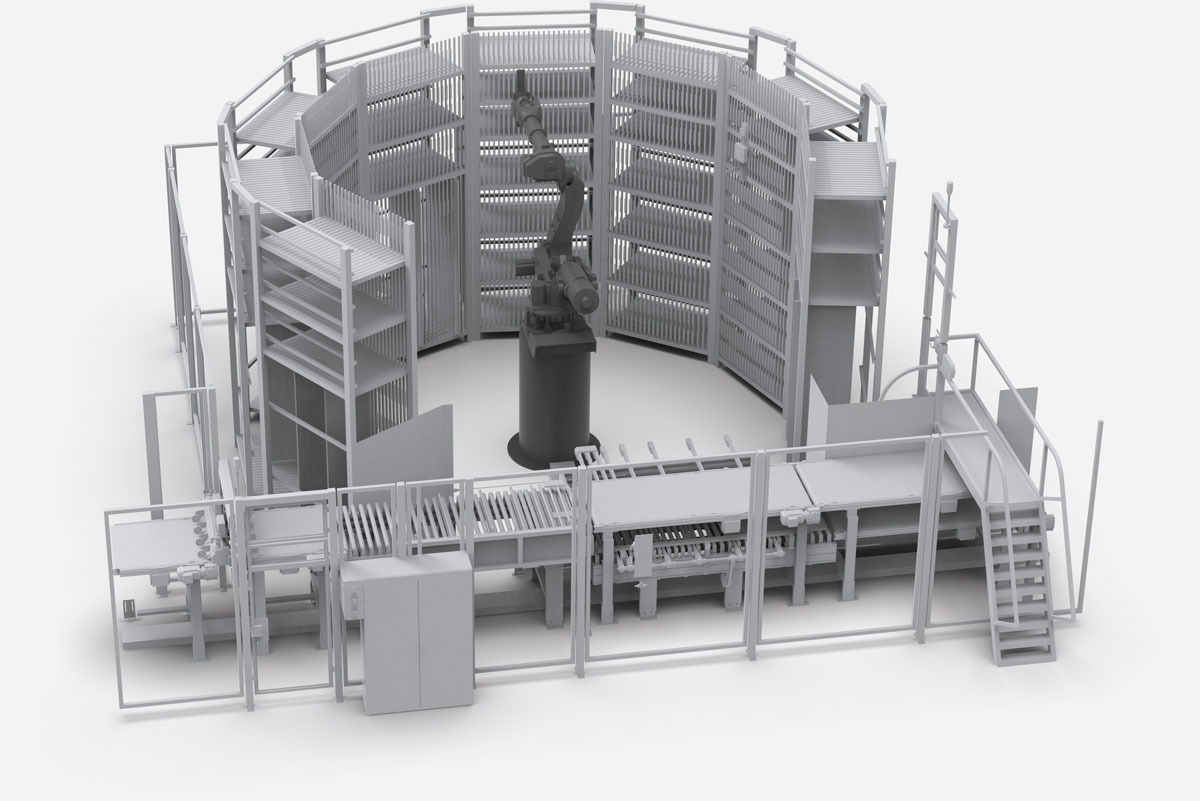
AC SERIES COMPACT AXES
LINEAR DRIVE FOR YOUR PROCESSES
MAXIMUM PERFORMANCE IN MINIMAL SPACE
The space-saving design of the AC series enables a high level of manufacturing flexibility and efficiency in the most varied application areas. It combines precise linear movement with powerful, integrated drives – and in a tiny amount of space. This allows it to be easily integrated into existing systems and combined together without problems. It thus increases the cost-effectiveness and performance of your automated processes. High speed and rapid acceleration also mean that you do not have to make any compromises in performance, even in tight space conditions.
OUR EXPERTISE – YOUR ADVANTAGES
- Optionally with safe torque off function
- Flexible control with IO-Link or CANopen
- Fast and powerful thanks to ball screw with BLDC motor
- High load capacity and service life thanks to linear guide with double rail carriage
Technical data | ||||
---|---|---|---|---|
Series | ACS40 | ACS60 | ||
Stroke [mm] | 100 | 150 | ||
Feed force max. [N] | 170 | 270 | ||
Speed max. [m/s] | 0.8 | 1,0 | ||
Acceleration max. [m/s2] | 20 | 17 | ||
Repeat accuracy +/- [mm] | 0.01 | 0.01 |
UL CERTIFICATION
GEH6000IL UND GED6000IL ZERTIFIZIERT FÜR DEN NORDAMERIKANISCHEN MARKT
The 6000 product family is the first gripper series worldwide to be UL-certified, ensuring not only the highest safety standards, but also compliance with North American regulations. This simplifies project planning and machine acceptance, saves time and money and ensures that our components operate smoothly in production plants. This certification gives you a clear competitive advantage: maximum security, increased efficiency and confidence in the quality of our solutions.
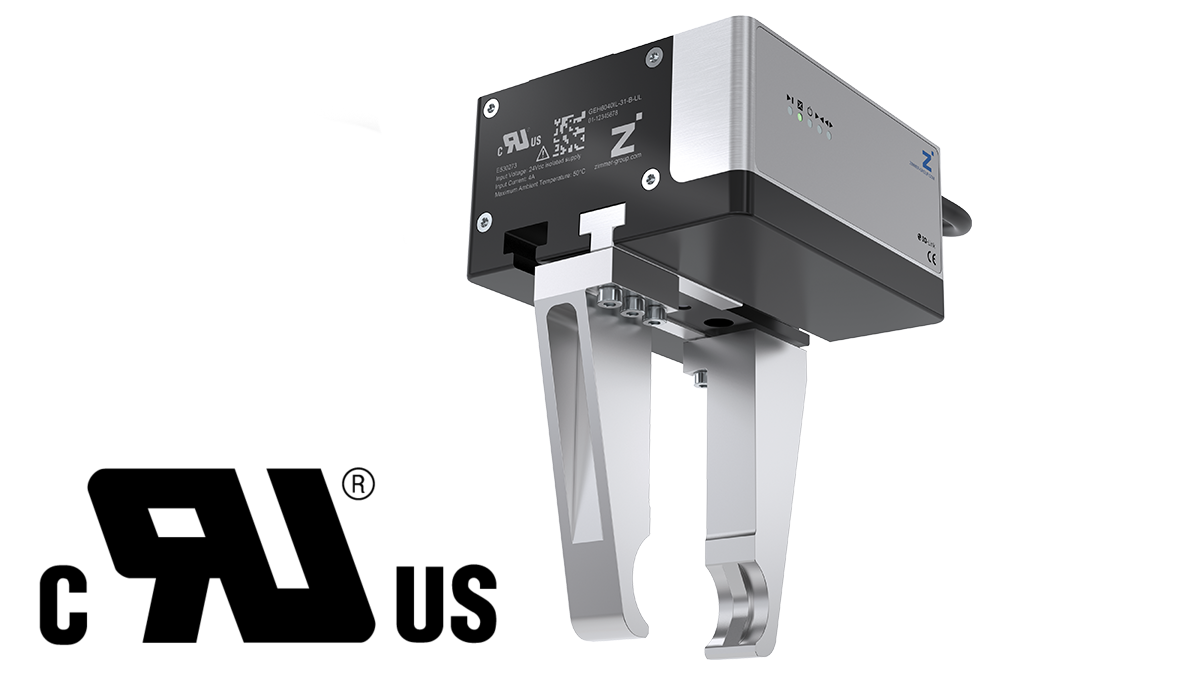
Zimmer Systems
Solutions for a huge range of industries
Experienced automation partner
With more than 40 years of experience in system solutions, we have established ourselves as a trusted and reliable automation partner for our customers. 140 employees continuously develop and integrate sustainable application solutions and automation concepts for all industries with state-of-the-art machines. For optimized productions rates and the highest quality standards.
EOAT for tires, wheels and rims
Zimmer Systems has exceptional expertise in the development, manufacture and integration of EOATs for handling tires, wheels and rims. With our experience and more than 5,000 hours of development work, we have been a reliable partner for end customers and equipment manufacturers in the tire industry since 2008. Our standardized gripper systems set new industry standards.
Battery handling – e-mobility solutions
We are leaders in the development of battery handling solutions for e-mobility. With more than 100,000 development hours since 2014, we are a trusted development partner for premium automobile manufacturers, OEMs and system manufacturers. Our tailored solutions ensure efficient and reliable automation in the battery manufacturing value chain.
Logistics and woodworking
TAILORED TO SPECIFIC APPLICATIONS
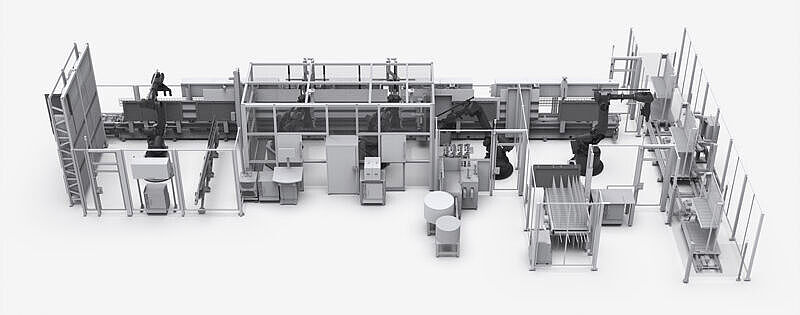
FURNITURE FRONT PROCESSING | BATCH SIZE 1 ROBOT-SUPPORTED DRILLING SOLUTIONS
Highly flexible shuttle circulation meets precision-compensated industrial robots with a drilling head for 17 vertical spindles and a buffer unit. Automatic loading and unloading is integrated into the customer's production control system.
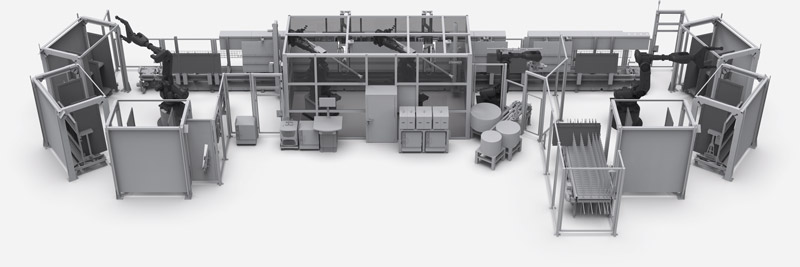
Furniture front processing system with shuttle circulation, precision-compensated industrial robots, a drill head with 17 vertical spindles, a milling spindle and a buffer adjustment device. The automatic loading and unloading of furniture fronts in shelf trolleys with safe shuttle storage ensures non-stop production.
Logistics solutions: Sorting and decoupling cells
This logistics system enables the automatic storage of manually stacked parts as well as the identification and control of the workpieces on the central conveyor belt. The parts are distributed efficiently across three identical storage cells to balance the load before being transported to the next process step.
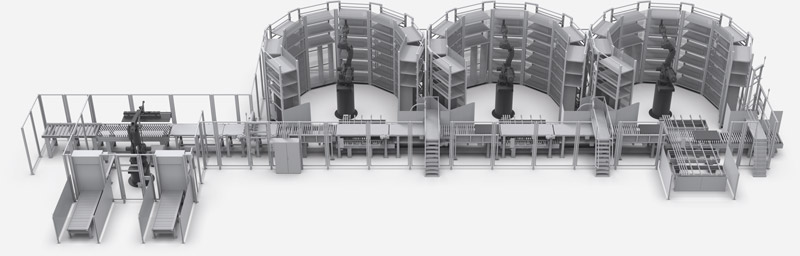
Tires, wheels and rims
Gripper systems
Handling systems from the experts
Tire manufacturing is a complex process that involves many steps from the green tire right through to the finished tire and rim. With increasing automation, we provide a wide range of handling solutions for different processes and production steps. The Zimmer Group has already realized a large number of projects. Our portfolio includes around 200 grippers and 15 standard grippers for the tire, wheel and rim industry.
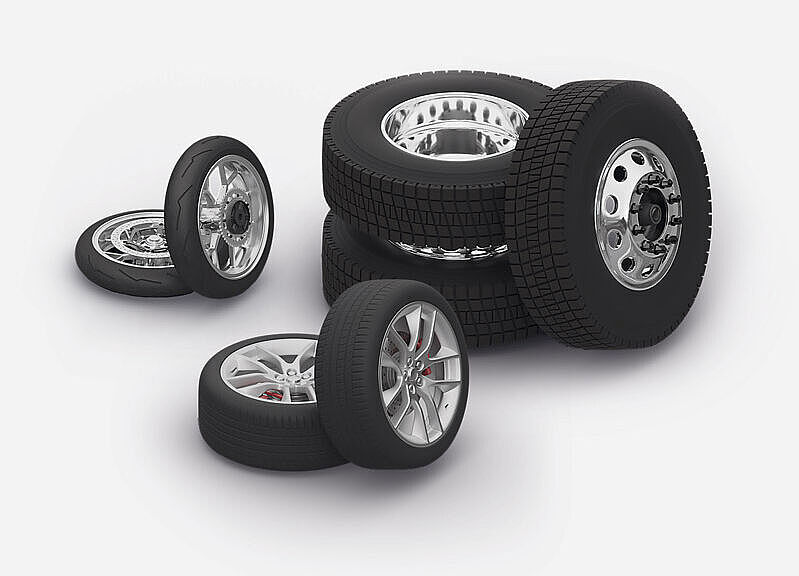
Technical data | ||||
---|---|---|---|---|
Tire type | Motorbike | PCR (Passenger Cars Radial Tires) | TBR (Trucks and Bus Radial Tires) | |
Outer diameter max. [mm] | 720 | 900 | 1250 | |
Outer diameter min. [mm] | 385 | 450 | 780 | |
Inner diameter max. [mm] | 520 (20") | 685 (27") | 710 (28") | |
Inner diameter min. [mm] | 204 (8") | 304 (12") | 450 (18") | |
Height max. [mm] | 215 | 400 | 460 | |
Height min. [mm] | 60 | 135 | 200 | |
Weight max. [kg] | 18 | 45 | 100 | |
Weight min. [kg] | 1,4 | 4 | - | |
Parts size variance | 8" - 20" | 12" - 27" | 18" - 28" |
EOAT solutions for batteries
Magnetic gripper
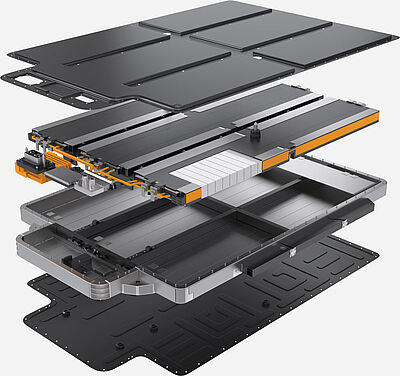
SOLUTIONS FOR BATTERY MANUFACTURING
The Zimmer Group is a development and system partner to major-name premium manufacturers and system manufacturers in battery production for electric vehicles. Whether for the production of cylindrical, prismatic or pouch cells. In partnership with you, we will develop the right solution – from the cell, through the packaging, right up to the module.
MAGNETIC grippers for cylindrical cells
The gripping of cylindrical cells requires precision interplay between the individual cells. The Zimmer Group has taken its standard magnetic gripper and developed a compact and powerful end-of-arm tool that holds the cells securely with a holding force of 65 N, even during high accelerations and emergency stops. With a low residual holding force of less than 1 N with deactivated magnets, the HPM2046 gripper ensures reliable set-down.
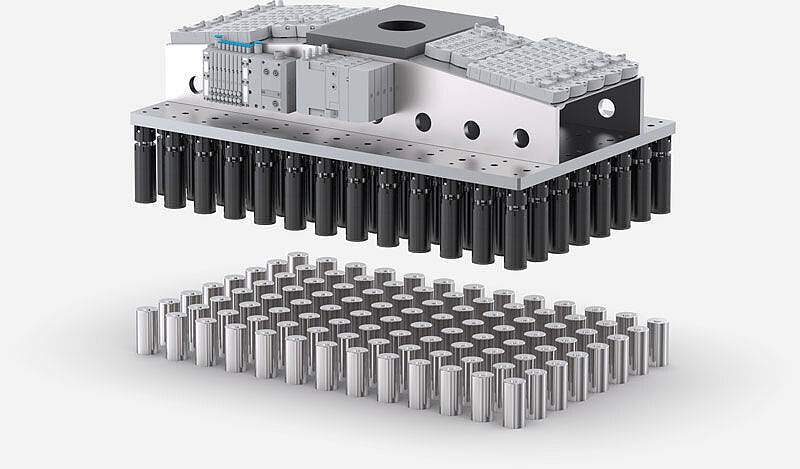
FAST ROUTES
INTRALOGISTICS SOLUTION
In a constantly changing world, companies are faced with the challenge of optimizing their intralogistics processes.
Our customized automation solutions ensure seamless integration into existing processes
and give you a real competitive advantage.
Bag gripper
Industry standard
HANDLING SYSTEM FOR BAGS
The Zimmer Group bag gripper is a one-of-a-kind end-of-arm system for handling bags filled with a wide variety of products. These include flour, fruit, vegetables, grain, fertilizer, chemicals, cement or numerous other products. At the same time, the materials of the bags to be handled also vary, including paper, plastic, jute and (woven) fabric.
PRODUCT ADVANTAGES
- Synchronous, pneumatically operated jaw movement and force conservation hold the workpiece centered and ensure long service life
- Large drive cylinders for fast cycle times of up to 20 cycles per minute depending on robot and travel path
- Optional functions such as lay-flat, intermediate layer handling and pallet handling
- Special forks for foodstuffs and hazardous/chemical materials
- Palletizing and depalletizing software for Yaskawa/ABB robots available
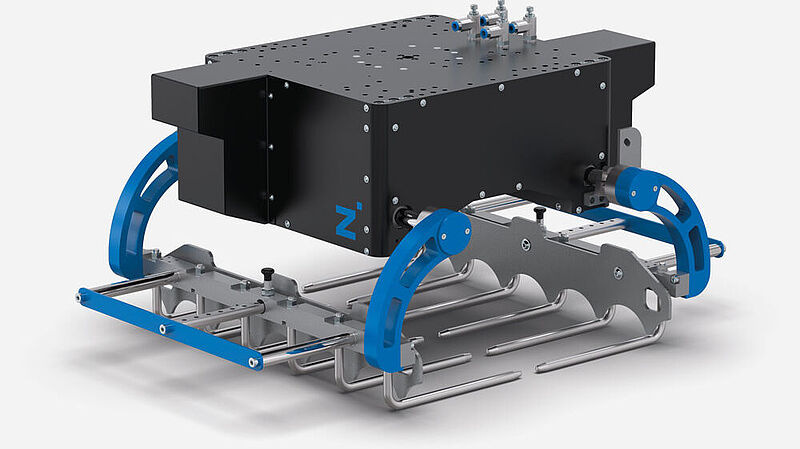
Technical data | ||||
---|---|---|---|---|
Part number | BAG137256 | BAG137855 | Z01SYS165171 | |
Product | Bag gripper | Bag gripper | Double bag gripper | |
Max workpiece weight [kg] | 25 | 50 | 25 + 25 | |
System weight [kg] | 45 | 55 | 115 | |
Dimensions max. [mm] [l x w x h] | 600 x 170 x 75 | 700 x 500 x 175 | 600 x 170 x 75 + 600 x 430 x 150 | |
Dimensions min. [mm] [l x w x h] | 600 x 170 x 75 | 700 x 300 x 100 | 600 x 170 x 75 + 600 x 170 x 75 | |
Open/closing time [s] | 0.6 | 0.6 | 0.6 |
MULTI-ITEM GRIPPER
VACUUM SUCTION CUP AND PARALLEL GRIPPER
Universal GRIPPER WITH object RECOGNITION
The Multi-item gripper combines a mechanical gripper and a vacuum gripper in one end effector. AI-supported image recognition and intelligent software take your bin picking tasks to the next level!
Vacuum gripper
The advantages of the gripper are particularly evident in bin picking with different surfaces and unsorted parts. The vacuum gripper is equipped with a vacuum maintenance system that ensures energy-efficient operation. The reliable medium supply and stable cylinder guidance enable precision applications, even with a wide variety of workpieces. Thanks to the interchangeable suction cups, you are ideally equipped for flexible tasks.
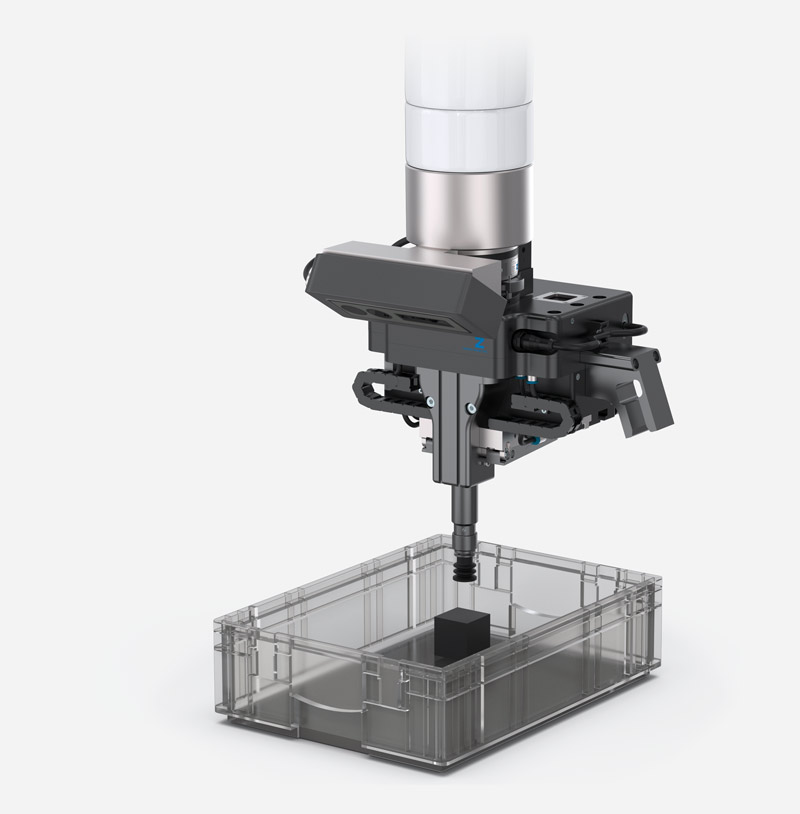
Parallel grippers
The vacuum gripper is complemented by a standard component that enables reliable and safe gripping. Thanks to URCap, installation and commissioning are just as easy as controlling the gripper. With extensive experience in handling technology, we have the expertise to tailor the gripper fingers to individual requirements.
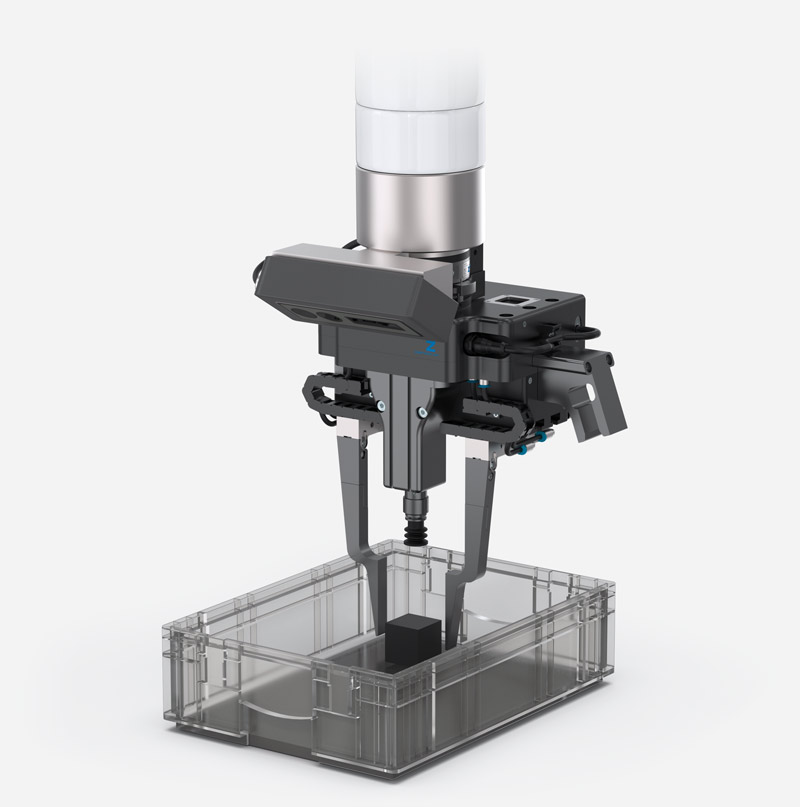
CLEANROOM CERTIFICATIONS
PRODUCTS WITH CLASSIFICATION
TÜV-CERTIFIED AUTOMATION TECHNOLOGY
Cleanrooms are divided into special cleanroom classes depending on the particle density and emissions. They are subject to strict, standardized requirements and are classified according to the degree of air purity. The maximum permissible particle concentration and the particle size play an important role here. Cleanrooms are divided into ISO classes 1 through 9, where purity class 1 represents the purest because it has the lowest possible particle concentration. After successful certification processes, more than 500 gripper and clamping elements from the Zimmer Group have been certified for cleanroom classes 2 to 6 in accordance with the international standard DIN EN ISO 14644-1 due to their low particle emissions.
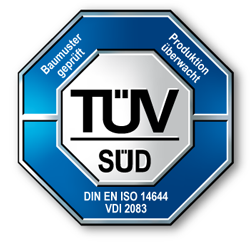
Technical data | ||||
---|---|---|---|---|
Series | Installation size | Variants | Cleanroom class | |
GEP2000 | all | all | 2 | |
GEH6000 | all | all | 4 | |
GED6000 | all | all | 4 | |
MGP800 | all | all | 6 | |
MK | all | all | 6 | |
MKS | all | all | 6 | |
GPP5000 | 5003 / 5004 / 5006 / 5008 / 5010 / 5013 / 5016 | -00 | 6 | |
-21 | 5 | |||
-AL | 4 | |||
GPD5000 | 5003 / 5004 / 5006 / 5008 / 5010 / 5013 / 5016 | -00 | 6 | |
-21 | 6 | |||
-AL | 4 |
SERIES AEPN
ELECTRO-PNEUMATIC UNIT
MOBILE AN INDEPENDENT
Our clamping and braking elements in particular provide high clamping forces with a low volume consumption and clamp just like our grippers or zero-point clamping systems as an NC variant when there is a pressure drop. The system bleeds as fast as lightning when the power fails thanks to our proven, integrated quick exhaust valve.
ELECTRO-PNEUMATIC POWERHOUSE
The electro-pneumatic unit can be combined with a variety of Zimmer Group products and enables the use of pneumatic products in areas where compressed air was previously not available. This opens up new possibilities in terms of design and safety and can offer a significant cost advantage.
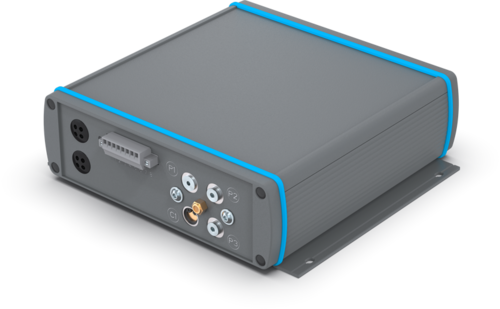
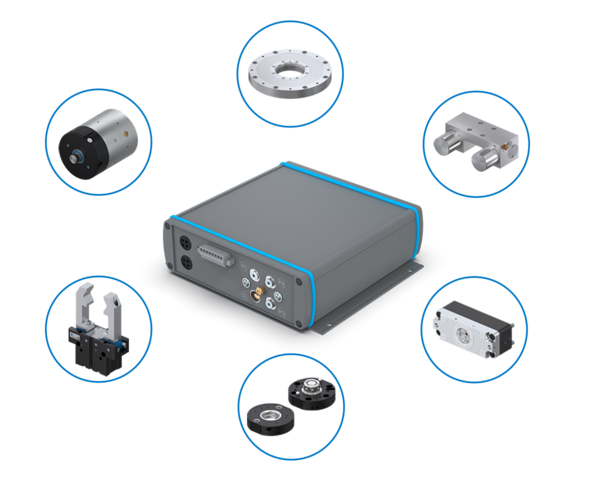
INTEGRATED SENSING AND EXTENDABLE
The unit is specially optimized to our components with low air consumption and enables optimized and energy-saving use thanks to a dynamic pressure setting. A pneumatic pressure of between 4 and 6 bar can be selected, which is then reliably regulated and maintained thanks to integrated sensing. If you upgrade to pressure storage, this can help to reduce the process time even further.
LIGHT & COMPACT
At the same time, this light and compact unit can be positioned close to consumers, thus enabling very fast opening and closing times. Thanks to the simple control and 24V technology, our product is predestined for mobile units with a battery supply, such as driverless transport systems. In addition, various process sequences can also be implemented thanks to the controllable valves.
DESIGN INCLUDED
When integrating the electro-pneumatic unit with our components, we will be happy to offer you a design of the switching times – and for braking elements, also the calculation of the braking distance taking into account your application data.
ALL-IN-ONE POSITION SENSOR
MFS02-S-KHC-IL
PRECISE and versatile
Discover our MFS02-S-KHC-IL position sensor. With IO-Link and an analog output, it extends our magnetic field sensor portfolio with continuous position measurement. The sensor features an impressive measuring range of up to 50 mm. With its space-saving installation in the C-groove, it can be integrated perfectly into any application. The exceptional resolution of 0.01 mm also enables the detection of defective parts (NIO), thus actively increasing your quality. Thanks to the dynamic teach-in function, which detects the standstill of the piston, three positions can be taught automatically.
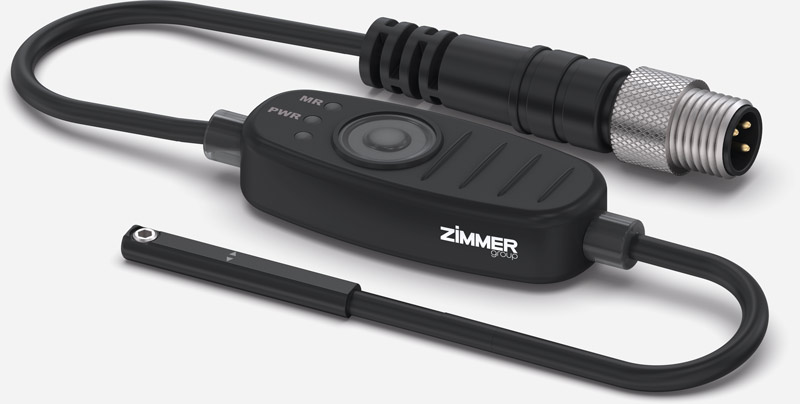
PNEUMATIC ROTARY CLAMPING ELEMENT
DKPS1000 SERIES
PNEUMATIC OR HYDRAULIC – THE CHOICE IS YOURS!
Increased performance requirements in tooling machines and an increased level of safety require powerful and innovative solutions. Following the successful market launch of our DKPS1000 series with pneumatic control and digital scanning, we are rounding off the extensive product range with additional installation sizes, thus closing the gap between all available sizes.
PRODUCT ADVANTAGES
- Torque absorption from shafts
- Safety clamping of the torque motor
- C-axis clamping
- Clamping and securing of swivel bridges
- Clamping of the spindle swiveling axis
SIMPLE STATUS SENSING
An efficient and fast process sequence is a requirement for all of our components and the DKPS1000 is no exception to this. The DKPS1000 can make use of its full potential thanks to the optional digital sensing. Additional safeties for switching times are no longer required.
HIGH HOLDING FORCES – WITHOUT ADDITIONAL AIR AND WITHOUT COMPROMISING CYCLE STABILIITY
The DKPS1000 series not only surpasses the non-pressurized holding force of rotary clamps available on the market; it also features an increased service life compared to the benchmark. Both of these properties equally ensure enhanced safety when it comes to safeguarding rotation and swivel axes. This also increases system availability.
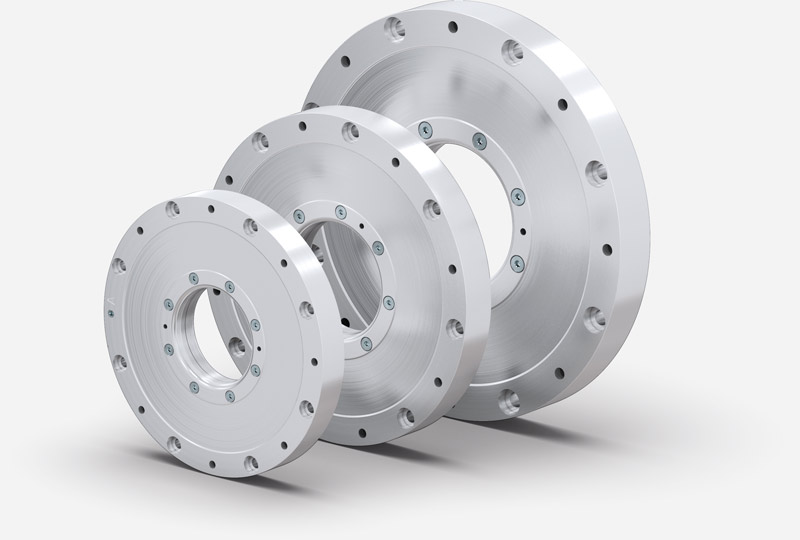
IO-LINK WIRELESS MODULES
ERROR-FREE communication
INTERFERENCE-FREE, SCALABLE, SECURE
Especially in robotics, the last robot axis often lacks an appropriate electrical interface for intelligent gripper components.
And in circulating systems, which are being used more and more frequently, it is missing completely. But why resort to external cable routing along the robot arm or circulation system and live with the associated disadvantages such as restricted freedom of movement, cable breakages and sources of interference when there is a straightforward solution?
The standardized IO-Link Wireless communication modules from the Zimmer Group enable trouble-free and secure communication of IO-Link signals, without any cabling, and guarantee wireless transmission of all required signals and information.